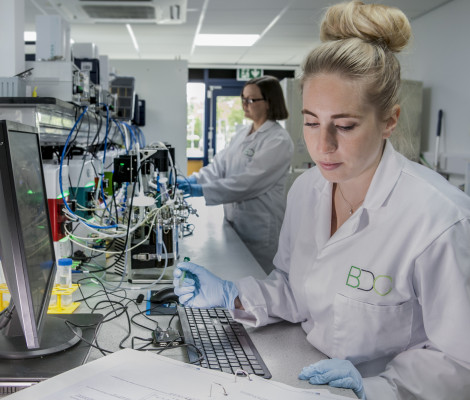
Fermentation facilities
We have several bioreactor systems, which allow the development and scale up of fermentation processes from 500 mL to 30 L.
Our bioreactor systems enable scale up of microbial fermentation up to 30 L. Our Bioscience Innovation Team is skilled in developing aerobic and anaerobic fermentation processes using a Design of Experiment approach. Fermentation parameters including pH, temperature, dissolved oxygen levels and feeding rates are optimised at each scale, from 500 mL to 5 L and 30 L.
Our fermentation facilities enable us to produce proteins and chemicals/biorenewables of high value, as well as assess the usefulness of novel sugar sources for fermentation. These might include food waste or lignocellulosic materials which have undergone physical, chemical or enzymic pretreatment.
Our fermentation facilities include the following:
Applikon multi-unit bioreactor system
This comprises eight 500 mL systems, each with its own controller unit, temperature and pH probes, off-gas analysers, and three variable speed pumps. Units are independently controlled using BioXpert V2 Advanced SCADA software. This system provides the capacity to run multiple experiments in parallel to facilitate swifter optimisation of growth / production conditions.
Sartorius 5 L and 30 L bioreactors
We have Sartorius bioreactors of 5 L and 30 L working volume. Both bioreactor types have controls for regulation of pH, temperature, dissolved oxygen (DO) and foaming throughout the microbial growth period. In addition, both vessels have systems in place for sterile sampling so that other analysis can be conducted mid-fermentation without damaging the integrity of the system. Data from the fermentation runs is collected by directly linking a computer to the bioreactor control panels for both vessels and can, subsequently, be analysed offline.
5 L bioreactor
The smaller of the Sartorius systems comprise two glass jacket vessels with a working volume of 5 L controlled by a Sartorius Biostat Bplus unit. For each unit, the temperature is controlled by a water jacket fed through a heater unit within the control unit. Additions to regulate the pH and apply antifoam oil are supplied through three peristaltic pumps attached to the control unit. The pH is monitored by a Hamilton Easyferm pH probe and the DO by a Hamilton Visiferm DO probe. Air is supplied via a ring sparger and DO is regulated using Rushton and/or marine impellers. Sterility of the vessel is accomplished using a Priorclave autoclave located within the fermenter unit.
30 L bioreactor
The largest of the Sartorius units has a 30 L working volume, with steam-in-place, controlled using a Sartorius Biostat Cplus unit. This is a stainless steel jacketed vessel connected to a Camptel steam boiler and a Frigomix cooling unit. This system can be sterilised at 121 °C using the adjacent steam generator; this also allows for in situ sterilisation of media, thus reducing potential for contamination. Subsequent temperature regulation is accomplished using the boiler and cooling unit in tandem. Similar to the 5 L vessels, pH and DO are monitored using Hamilton Easyferm and Visiferm probes respectively. DO can be modulated through the use of a back pressure valve. Any additions may be made via a peristaltic pump arrangement and air is supplied via a ring sparger.
We have several bioreactor systems, which allow the development and scale up of fermentation processes from 500 mL to 30 L.
In our process development laboratory we have a 480sqft flexible hall, if you have a piece of equipment that needs the right infrastructure and dedicated space to make it work then our flexi hall could be the right place for it.
Our microbiology laboratory offers a range of equipment allowing users to safely handle, store and work with a variety of aerobic and anaerobic microbes at ACDP hazard category II level.
We have established a set of molecular analysis labs to enable a variety of genetic analysis applications to be carried out.